Plastic Pallets Decrease Downtime, Increase Bottle Handling Efficiencies
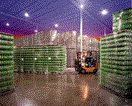
Schmalbach-Lubeca Plastic Containers USA (Manchester, MI) is a major supplier of plastic bottles to the beverage industry. One of the company's leading customers, Pepsi-Cola, asked S-L to switch from wood to plastic pallets for the delivery of empty bottle shipments to its bottling plants. Pepsi had undertaken an analysis of the advantages of wood versus plastic pallets and decided that plastic offered some important operating benefits.
In response to the Pepsi request, Schmalbach-Lubeca began to convert to plastic pallets. S-L opted to install 44 x 56-in plastic beverage pallets manufactured by Cookson Plastic Molding Corp. (Latham, NY). Currently, all the bottle supplier's U.S. plants use these plastic pallets.
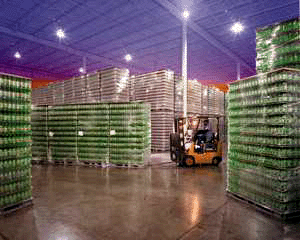
One Plant's Perspective
Schmalbach-Lubeca's New Castle, DE, plant produces approximately 700,000 16-oz and 20-oz soft drink bottles/day for regional Pepsi bottlers. Todd Miller, plant manager at New Castle, said, "The plastic pallets have helped both Schmalbach-Lubeca and Pepsi decrease downtime and increase efficiencies."
At New Castle, two high-speed blowmolding machines produce bottles that are then automatically conveyed through a labeler and into a bulk palletizer where they are stacked in tiers. A strapping machine stabilizes the pallet load, and then the loaded pallet is conveyed to a stretchwrapper. The stretchwrap film serves to further stabilize the bottles and protect them from dust and other air-borne particles during storage and shipment. The finished pallets are moved three or four at a time by forklift truck through warehousing and delivery vehicle loading operations.
"Downtime issues were central to the decision to go to plastic," said Miller. "Just a little blip in the line can cause you to shut down a machine. And that's expensive because the margins are very small. The goal is to get the most volume out of a day."
The wood pallets had splinters and nails—things that can cause jam-ups in conveyors and palletizers. Miller also noted that the plastic pallets don't carry the repair expense problems associated with wood pallets. The one-piece Cookson plastic pallets were selected by Schmalbach-Lubeca because of their demonstrated resistance to damage. Sorting broken wood pallets used to be a full-time job at the plant. Now that manpower can be assigned to other tasks.
Another advantage is the greater consistency of the plastic pallet structure. Mary Jean Parks, material/customer service coordinator for S-L Newcastle, commented, "The plastic pallets are much more consistent than wood, so we get much more stable loads and a lot less damage. If a pallet is a little crooked, the bottles start shifting, and the entire load leans. We can't ship it because the customer can't depalletize it. Unstable loads that do reach the customer are returned—leaving the customer short and sometimes incurring monetary penalties for Schmalbach-Lubeca."
No equipment changes were needed to achieve conversion from wood to plastic because the plastic pallets are equivalent in size to the old wood ones. As Todd Miller concludes, "The investment in plastic pallets was worth it. They will more than pay for themselves based on their efficiency and long life expectancy. And most importantly, the customer is happy."
For more info about plastic beverage bottles: Schmalbach-Lubeca Plastic Containers, Manchester, MI. Tel: 734-428-9741; Fax: 734-428-4622.
For more information about plastic pallets: Cookson Plastic Molding Corp., Latham, NY. Tel: 518-783-3194; Fax: 518-783-0004; www.cooksonmhd.com
Edited by Judy Rice, Managing Editor, Beverage Online